Overcoming the challenges of siloed infrastructure in Industrial Internet of Things (IIoT) environments involves strategic, technological, and organizational efforts. It aims at data sharing, collaboration, enhancing connectivity, and interoperability across different systems and departments. However, the presence of data silos can restrict progress, leading to a lack of communication and decreased productivity.
What is Siloed Infrastructure in Industrial IoT?
A siloed infrastructure refers to a scenario where different Industrial IoT devices, systems, and data sources within an industrial environment operate independently, with limited or no interoperability or communication between them. It occurs due to various factors, including the use of proprietary technologies, lack of integration standards, or organizational barriers. Siloed infrastructures in Industrial IoT environments can lead to several challenges and inefficiencies, impacting the overall performance and effectiveness of industrial operations.
What Impact Does a Siloed Infrastructure Have on Business Goals?
In general, siloed infrastructures are more commonly associated with negative impacts on business operations and goals. However, there can be situational benefits as well. Both are listed below.
Positive Impact of Siloed Infrastructure
- Specialization: Departments or teams can develop deep expertise in their specific domain, leading to high-quality outcomes in those areas.
- Control and Security: Tight control over data and processes within silos can, in some contexts, enhance security and compliance by limiting access.
- Simplified Management Within Silos: Within their boundaries, silos can simplify management and decision-making by reducing the complexity of having to consider broader organizational impacts.
Negative Impact of Siloed Infrastructure
- Reduced Operational Efficiency: Inefficiencies due to poor communication, redundant efforts, and cumbersome cross-departmental processes.
- Hindered Innovation: Limited knowledge sharing and collaboration reduces the organization's capacity for innovation and rapid adaptation.
- Poor Data Utilization: Inconsistent data and underutilization of data across silos limit insights and optimization opportunities.
- Impaired Decision-Making: Lack of comprehensive visibility and slower responses to market changes due to isolated information.
- Increased IT Complexity and Costs: Complex integration challenges and higher operational costs from maintaining multiple systems.
- Security and Compliance Risks: Increased vulnerability to cyber threats and challenges in maintaining regulatory compliance due to inconsistent security protocols across silos.
7 Best Practices to Overcome the Siloed Infrastructure in Industrial IoT
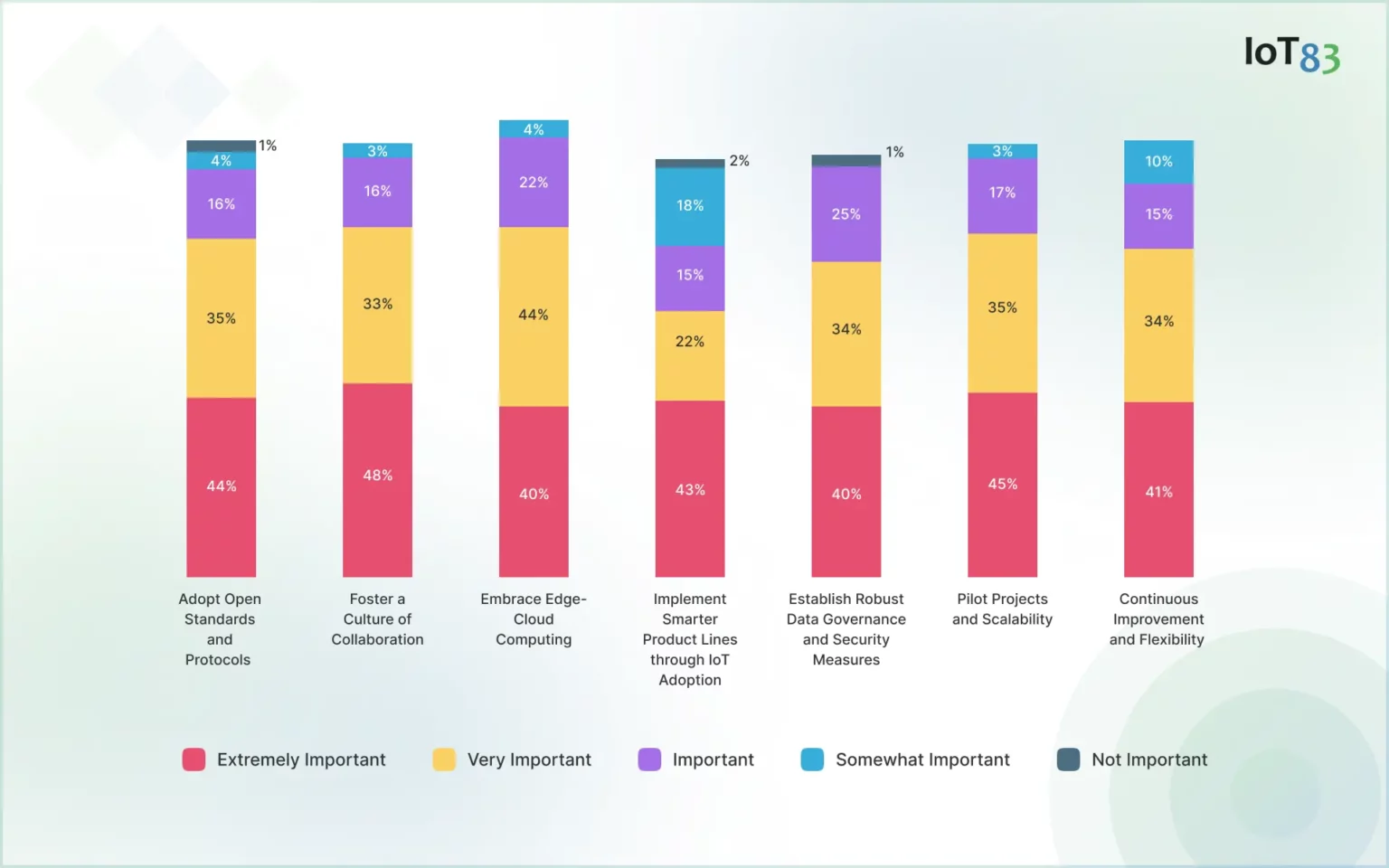
1. Adopt Open Standards and Protocols:
- Use standardized communication protocols such as MQTT, AMQP, or OPC UA to facilitate easier integration and data exchange between devices and systems.
- Leverage industry standards for data modeling and interoperability, such as those from the Industrial Internet Consortium (IIC) or the International Society of Automation (ISA), to ensure compatibility and ease of integration efforts.
2. Foster a Culture of Collaboration:
- Encourage cross-departmental collaboration to break down silos within the organization. This can involve creating interdisciplinary teams focused on IoT projects that span different operational areas.
- Promote knowledge sharing through regular meetings, workshops, and training sessions. It can help ensure all stakeholders understand the benefits of integrated IIoT systems and how to leverage them effectively.
3. Embrace Edge-Cloud Computing:
- To realize the value of business transformation, OEMs must integrate this new IoT data into smart applications and smart solutions or this IoT Edge data.
- Edge Computing processes data closer to where it is generated, reducing latency and bandwidth use and enabling real-time decision-making. This can help integrate processes across different locations and systems by providing a standardized approach to data processing and analytics.
4. Implement Smarter Product Lines through an IoT Platform:
- Deploy an IoT platform that can act as a middleware layer to connect disparate systems, allowing for data aggregation, visualization, and analysis in a centralized location.
- Choose platforms that support multi-protocol integration and can interface with both legacy systems and newer IoT devices to bridge the gap between old and new technologies.
5. Establish Robust Data Governance and Security Measures:
- Address data ownership, access controls, and quality standards with a comprehensive data governance framework. Ensure data is shared and used effectively across the organization.
- Prioritize cybersecurity by adopting best practices for securing IoT devices and networks, including regular updates, encryption, and intrusion detection systems, to protect against threats that could exploit interconnected systems.
6. Pilot Projects and Scalability:
- Demonstrate the value of integrated systems with pilot projects and gather insights before scaling up. This allows for identifying potential issues and proving the concept in a controlled environment.
- Plan for scalability by choosing solutions and architectures that can grow with your IoT deployment, ensuring the system can handle increasing data volumes and more complex integrations as your Industrial IoT ecosystem expands.
7. Continuous Improvement and Flexibility:
- Adopt a mindset of continuous improvement, where feedback from IoT systems is used to refine processes and integration strategies over time.
- Stay flexible and open to adopting new technologies and practices as the Industrial IoT landscape evolves, ensuring your infrastructure can adapt to future needs and opportunities.
By addressing these areas, organizations can overcome the challenges of siloed Industrial IoT infrastructures, paving the way for more efficient operations, better decision-making, and enhanced innovation. The need of the hour for OEMs is to update traditional unconnected products with connected data and then add this IoT data into new OEM services like asset performance monitoring, asset Remote Management, predictive maintenance, optimized field operations, and even new business models like equipment as a service.
Application Enablement Platform can help teams focus directly on creating this new differentiation without the overhead delays and risks of the underlying technology. It can be the best solution to enhance interoperability, such as adopting industry standards, implementing integration platforms, and fostering collaboration across different departments and teams. Here are various ways an Application Enablement Platform can help you get out of a siloed infrastructure.
- Support cross-functional communication
- Consolidate data into a single repository, Centralize data
- Retire legacy systems
- Establish a data governance framework
- Defined and transparent processes
All of this works to unblock your path to a powerful competitive advantage for your business now and for your future. Let's connect to discuss siloed infrastructure solutions further, specifically for your business needs.